Summary
The R&D team for Cannon Afros has studied and developed a new type of VIP panel, based solely on waste or end-of-life rigid foam powders, with insulating capacities 2 to 5 times better than the original foams. This demonstrates that thermoset foams, which are difficult to recycle and reuse, can be given new life in a simple and economical way.
Author: Dr. Eng. Maurizio Corti, Technology and R&D Director, Cannon Corporate
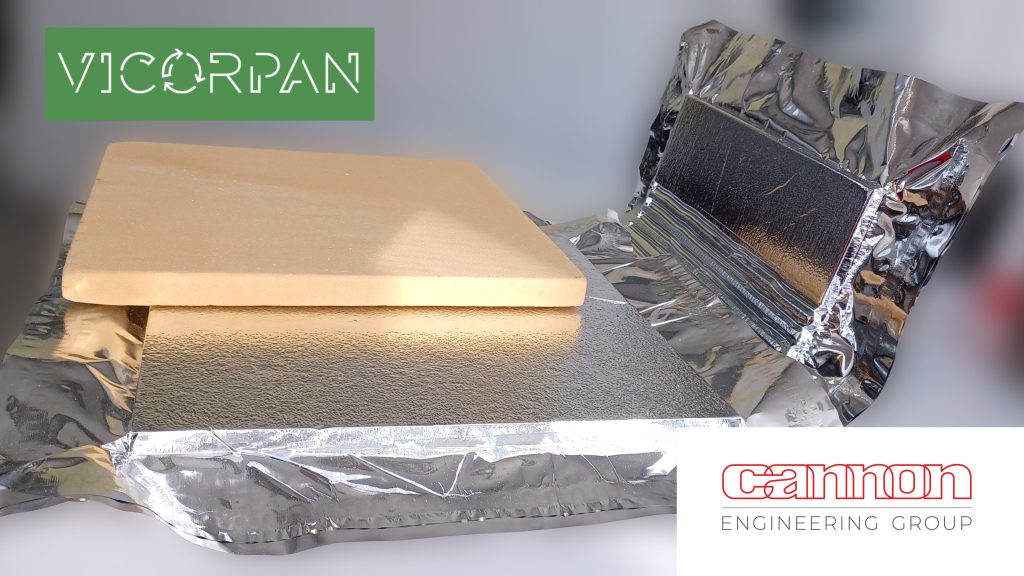
Premise
Thermal insulation has long been achieved using layers of materials with very low mass-to-volume ratios and high porosity. These materials contain numerous small air pockets interposed between finely intertwined solid constituents.
In this configuration, heat transfer by conduction — via contact between adjacent solid components — is significantly reduced due to thin thermal bridges formed at the contact zones. These bridges have extremely limited and fragmented contact surfaces.
With traditional thermal insulators, the primary heat transfer mechanism, accounting for 65% to 85% of total heat transfer, happens through convection. This occurs from the presence of air within the porous materials, where heat is transferred via thermal agitation of atmospheric gas molecules.
Current regulations for buildings and cold cycles (e.g., refrigerators, refrigerated cells) demand ever-increasing thermal insulation capacity to reduce energy consumption and ensure energy neutrality between the energy consumed and the energy produced from renewable sources.
To drastically reduce heat transfer in traditional porous and/or finely reticulated materials, they are configured into vacuum-insulated panels (VIPs). VIPs are composed of an internal structure, the “core,” formed of fine particles aggregated or compacted to withstand atmospheric pressure. The core is then placed under a vacuum to remove the gases responsible for convection and sealed within envelopes or pouches made from laminated films consisting of alternating layers of plastic and metal (normally aluminum).
By removing most gases from the porosities, heat transfer via gas molecule agitation is minimized, resulting in a structure with far greater thermal insulation than the same material exposed to atmospheric pressure.
Currently, there are two types of VIPs available on the market:
- Cores formed from highly compacted fine glass fibers;
- Cores made from submicrometric grains of silica fume (expanded porous silica).
The most commonly used glass fibers must have a diameter greater than 5 microns to avoid being classified as carcinogenic. However, ongoing studies are investigating the potential hazards of fibers with larger dimensions.
VIPs with glass fiber cores typically exhibit a thermal insulation coefficient (λ) of around 4 mW/m°K. If the fibers are aligned in common directions, curled, or extruded with a non-cylindrical cross-section, the panels can achieve coefficients as low as 2 mW/m°K.
Due to the environmental hazard posed by their dispersion, VIPs with glass fiber cores are currently, and almost exclusively, produced in China.
VIPs based on silica fume, on the other hand, consist of nearly spherical floccules made from expanded silicon rendered highly porous by manufacturing technology. This porosity ensures good insulation even when gas and vapor penetrate the panel after several years. However, the structure of the silica fume aggregates is highly friable, requiring stabilization using a significant percentage of glass fibers to withstand the compression exerted by atmospheric pressure.
Silica fume VIPs achieve a thermal transmission coefficient (λ) of 4-6 mW/m°K.
Although already widespread, VIPs made from glass fiber or silica fume cores also present critical issues and challenges:
- If the sealed film is perforated during handling or use, their insulation capacity is immediately lost.
- If the film is damaged and releases even a small amount of its content, it can contaminate the environment with core-forming particles — particularly sharp and thin glass fibers. These may deposit and accumulate in the lungs or in machinery filters and air conditioners, becoming a persistent pollutant with respiratory health risks which are currently under investigation.
- The density of existing cores is high (around 200-300 kg/m³), making these panels much heavier than foams typically used for insulating refrigerators and buildings.
- Recycling and reusing these panels and their cores is extremely difficult and complex because, at the end of their life, their envelopes are broken or shredded, inevitably releasing fibers and powders into the environment.
- The energy content of VIP panels with glass fiber or silica fume cores, in terms of CO2 equivalent, is very high and requires substantial energy to produce the glass or silica fume used to form the cores.
Technologies Developed by Cannon for the LIFE 20 CCM/IT/VICORPAN Project
To address these challenges, Cannon, in partnership with BASF and EPTA, has developed and refined lightweight and easily recyclable VIPs with cores made from open-cell polyurethane foam. These panels have proven to be lightweight, durable, moldable, and capable of maintaining a thermal insulation coefficient (λ) = 6–7 mW/m°K. This insulation capacity is highly interesting, especially when compared to the best polyurethane foam, which has a coefficient λ ≥ 18–19 mW/m°K.
These panels are very light and fully recyclable compared to VIPs made with glass fiber or silica cores and can be shaped as needed. The panels have been studied, shaped, and characterized for their application to commercial refrigerators produced by EPTA, using cores formulated by BASF. They are currently being applied to supermarket refrigerators and freezers by EPTA, demonstrating ease of use while significantly improving freezer efficiency. The BASF foam has proven capable of withstanding atmospheric pressure and is much more suitable than traditional cores (glass fiber or silica fume) for shaping and inserting into refrigerator walls.
Shredding tests simulating end-of-life refrigerator disposal have shown that these panels are fully recyclable without interfering with current end-of-life treatment technologies. These processes allow the recovery of all plastic, metal, and foam components in granular form.
Groundbreaking Technology for Recycled and Reused VIP Panels Demonstrated and Patented by Cannon Afros with Minimal Environmental Impact
Recently, technicians in Cannon’s R&D laboratory have discovered a way to further advance the LIFE20 VICORPAN project, achieving highly significant technological results for recycling and reusing polyurethane foams.
This newly studied technology is currently patent pending and enables the production of VIP panels based on cores made from recycled foams, primarily low-density rigid polyurethane foams.
Even foam scraps, including those with poor insulation performance, reassembled into vacuum panels, achieve thermal transmission coefficients far superior to the original insulation foam.
Depending on the characteristics of the source material, the milled material, and the processing and aggregation methods, the methodology developed by Cannon Afros allows for the production of flat or shaped VIP panels with insulation properties that are at least double those of the original core materials and can reach values up to five times better. In the optimized configuration, the thermal insulation coefficient (λ) is 6–7 mW/m°K.
Methodology for Producing VIP Cores Based on Particles or Powders of Rigid or Semi-Rigid Foam with Optimal Thermal Insulation Conditions
The developed methodology allows for the production of flat or shaped VIP panels.
The vacuum-maintained part of these panels consists of powders obtained by cutting and grinding rigid or semi-rigid polyurethane or phenolic foams.
The powders must, however, be produced and selected based on a maximum size, which depends on the cell configuration of the foam they originate from to ensure optimal thermal insulation performance. These powders can be aggregated using appropriately dispersed binders or by employing conventional physical binders such as glass or cotton fibers.
Once the binder is dispersed, the core’s shape is created through mold pressing.
Through pressing, the desired shape and necessary resistance are imparted to the core before it is inserted into the sealing envelope. Its mechanical resistance must ensure that it does not deform under atmospheric pressure once vacuum sealed.
It must also allow the core to be bent or formed into shapes, such as cylinders, depending on application requirements.
For sealing, the core and components of the not-yet-sealed envelope are appropriately positioned on a masking fixture to ensure correct placement for the core and the two sides forming the envelope. These are then placed into a vacuum chamber, where air and gases from the cores are evacuated using a vacuum pump.
Within the chamber, vacuum conditions are maintained for the time necessary to evacuate the required amount of gas to achieve the product-enhancing λ value. Then, within the vacuum chamber, the still-open edges of the envelope are sealed using heated blades at controlled temperatures.
Structure of the Source Powder Material in Foam Form
Rigid or semi-rigid foams are materials that do not recover their original shape when subjected to significant deformation.
These foams can feature closed cells, meaning each cell is separated from adjacent ones by membranes that seal their contents. Specifically, (see Figure 1), individual foam cells are characterized by polyhedral structures separated by flat membranes and outlined by polygonal edges (struts) thicker than the membranes.
Semi-rigid foams, on the other hand, have open cells, meaning their membranes are partially formed or perforated. They are characterized by polygonal edges (struts) that are thicker and stiffer, with nodes connected to the struts via broad radii. Membranes may still be present between struts but feature central perforations caused by tearing during foam expansion.
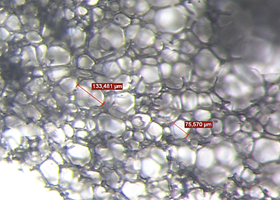
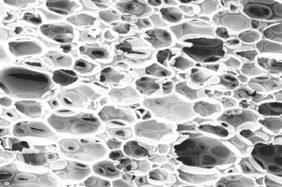
Characterization and Selection of Particles Forming These Powders
The powder used to form the VIP cores consists of foam particles with broken cells (see Figure 3). These particles are typically generated during industrial cutting and shaping processes for rigid or semi-rigid foam using toothed tools. Alternatively, the powder can be produced by grinding entire pieces of foam: these parts are first reduced to small pieces using granulators and then passed through special pulverizers. The resulting powder must consist of over 95% by mass of broken foam cell components.
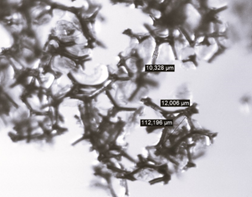
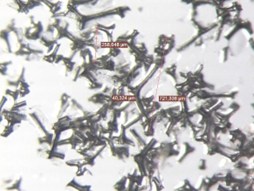
The two images illustrate powder particles with highly different structures, representing boundary cases under consideration.
If the powders are derived from insulation foam waste, they may also contain chips from covering layers. The presence of granules and floccules from these layers increases the thermal conductivity of the conglomerate forming the panel core. However, it has been demonstrated that even a significant percentage of parts from covering layers can be accepted while still achieving excellent insulation coefficients.
Furthermore, grinding operations must be conducted to ensure that closed cells are broken. The foam must therefore be ground according to the average size of the cells.
Characterization and Selection of the Core’s Compression Resistance Properties
A core made of aggregated powder must possess mechanical characteristics that:
- Allow machining with toothed tools to produce shaped panels.
- Resist disintegration when a vacuum is applied to remove air flow from the porosity.
- Withstand atmospheric pressure, preventing deformation or damage to the edges once sealed within the film.
Mechanical characteristics are measured using an indentation test, where a shaped tip applies local pressure on the core before it is vacuum-sealed.
While this technology was being developed, the optimal method involved applying a layer of natural or synthetic fibers of a nonwoven fabric to the cores. This layer protects the core during handling and packaging.
Folding and Circular Bending without Interrupting the Continuity of Insulation
A known problem for applying VIP panels as insulation for box-like structures is the presence of thermal bridges deriving from the edges of these panels which are coated with the sealing film.
These edges conduct heat much more than the panel’s surface and therefore constitute important thermal bridges.
To overcome this problem, it is possible to prepare suitable shapes for the cores so that they can be bent up to 100 degrees, thus avoiding these thermal bridges.
Similarly, it is possible to shape VIPs in cylindrical forms to insulate, for example, hot or chilled water containers.
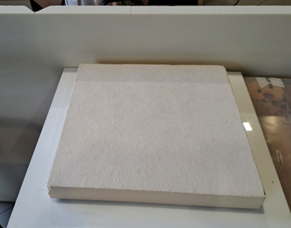
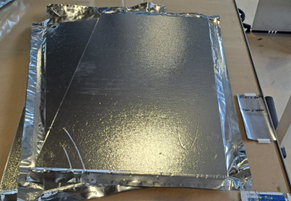
Conclusions
The VIPs developed and produced for the LIFE20/CCM/IT/VICORPAN project with open-cell foam, tested and applied in partnership with BASDF and EPTA, have proven to be lightweight, high-performing, and stable over time, so they can be applied to commercial and domestic refrigerators as an alternative to the current VIP panels that pose considerable problems in terms of recyclability and potential environmental pollution during disposal.
The VICORPAN VIPs made of open-cell foam have a lambda of 6-7 mw/m°K, can be produced in very large sizes, and can be shaped without thermal bridges.
They have been adapted and are currently being tested in insulation structures containing reinforcements and attachments such as commercial refrigerators and refrigerated trucks.
They are light (60-70 g/liter) and are perfectly suited to disposal technologies used for current commercial and domestic refrigerators without causing any pollution.
They are also finding interest in industrial applications where lightness is important, such as in refrigerated trucks.
The LIFE 20 VICORPAN project has made it possible to demonstrate a new, unprecedented technology for recycling and reusing polyurethane foam, either waste or end-of-life, in the form of VIPs composed of recycled powder with an insulation capacity equal to or greater than twice and up to five times that of the original foams with an excellent 6-7 mw/m°K. The R&D technical team at Cannon Afros is proud of the results found and their applicability in solving an important problem regarding recycling and reusing polyurethane foams.