In the dynamic world of polyurethane manufacturing, precision and efficiency are paramount. Since 2022, Cannon has set a new standard with OptiWise, an innovative predictive maintenance system integrating Artificial Intelligence (AI) and IoT capabilities. This cutting-edge solution has been developed to enhance the performance and reliability of crucial components such as mixing heads and pumps, pivotal for seamless operation in foaming machines.
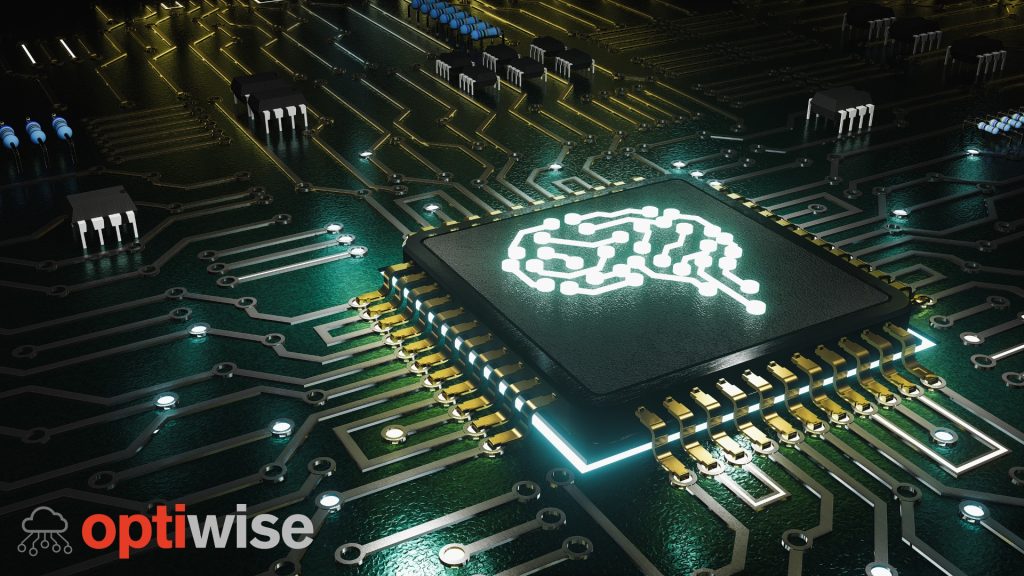
The power of predictive maintenance
Predictive maintenance relies on advanced data analytics and machine learning. By harnessing a network of sensors embedded in high-pressure mixing heads and pumps, OptiWise continuously monitors key operational parameters. These sensors collect real-time data, which is securely transmitted to the cloud for analysis. Here, sophisticated Artificial Intelligence algorithms detect anomalies and predict potential failures well in advance. This proactive approach allows maintenance teams to schedule interventions precisely when needed, preventing costly downtime and ensuring uninterrupted production.
Mixing heads and pumps is critical to PU foaming machines. OptiWise empowers Cannon clients to detect and address issues before they escalate, optimizing operational uptime and reducing maintenance costs.[1]
Innovative sensor technology
Central to OptiWise is Cannon’s proprietary “Talking Head” technology, a patented mixing head developed in 2019 and now successfully used in countless applications. This mixing head features an array of sensors to monitor performance metrics throughout the equipment’s lifecycle. Continuous data collection and analysis refine the predictive maintenance algorithm, ensuring its adaptability and reliability.
Optimizing the PU dosing unit with AI
The integration of AI within Cannon’s dosing unit elevates predictive maintenance to a new level. Advanced machine learning algorithms can analyze real-time data from devices specifically designed for vibration analysis applied to dosing unit pumps and motors, and identify anomalies that deviate from standard operating ranges. Data from different types of vibrations are collected into a cloud, where artificial intelligence software analyzes and processes them, developing predictive maintenance algorithms. This data-driven approach allows for reducing operational costs and downtime, making operations more sustainable and competitive.
Tailored solutions for every need
Recognizing the diversity of manufacturing environments, OptiWise offers customizable features. During an initial “training period”, the system establishes baseline operational parameters specific to each dosing machine. This personalized approach ensures that abnormal trends are promptly identified and addressed, further optimizing performance and extending equipment lifespan.
Unlocking the potential
OptiWise transcends traditional maintenance practices, offering a multitude of benefits:
- Preventative Maintenance: Identifying and addressing issues before they affect production.
- Enhanced Efficiency: Maximizing uptime and production speed.
- Longevity: Extending the lifespan of critical components.
- Cost Efficiency: Streamlining maintenance schedules and spare parts management.
- Future Readiness: Embracing the transformative potential of IoT and Industry 4.0.
As Cannon continues to innovate, their predictive maintenance service stands at the forefront of predictive maintenance technology, redefining standards in polyurethane manufacturing. Embrace the future of smart manufacturing with OptiWise, where proactive maintenance meets unparalleled performance.
For more information on how OptiWise can optimize your manufacturing process, visit Cannon’s official website https://www.cannon.com/ or contact our dedicated team today.