From advanced protection for luxury cars to becoming the industry standard
Reaction injection molding (RIM) coating was originally introduced as a clear layer applied to safeguard the wood veneer of luxury cars, at a time when wood use was still widespread in the automotive industry. Since then, wood has largely been eliminated from automotive production in favor of thermoplastic materials, due to increasing safety and impact standards, but RIM coating remains and with each passing year becomes more important as an application. Covering interior and exterior trim parts, it gives that pleasant aesthetic, glossy appearance we expect from our cars and brings a host of protective benefits.
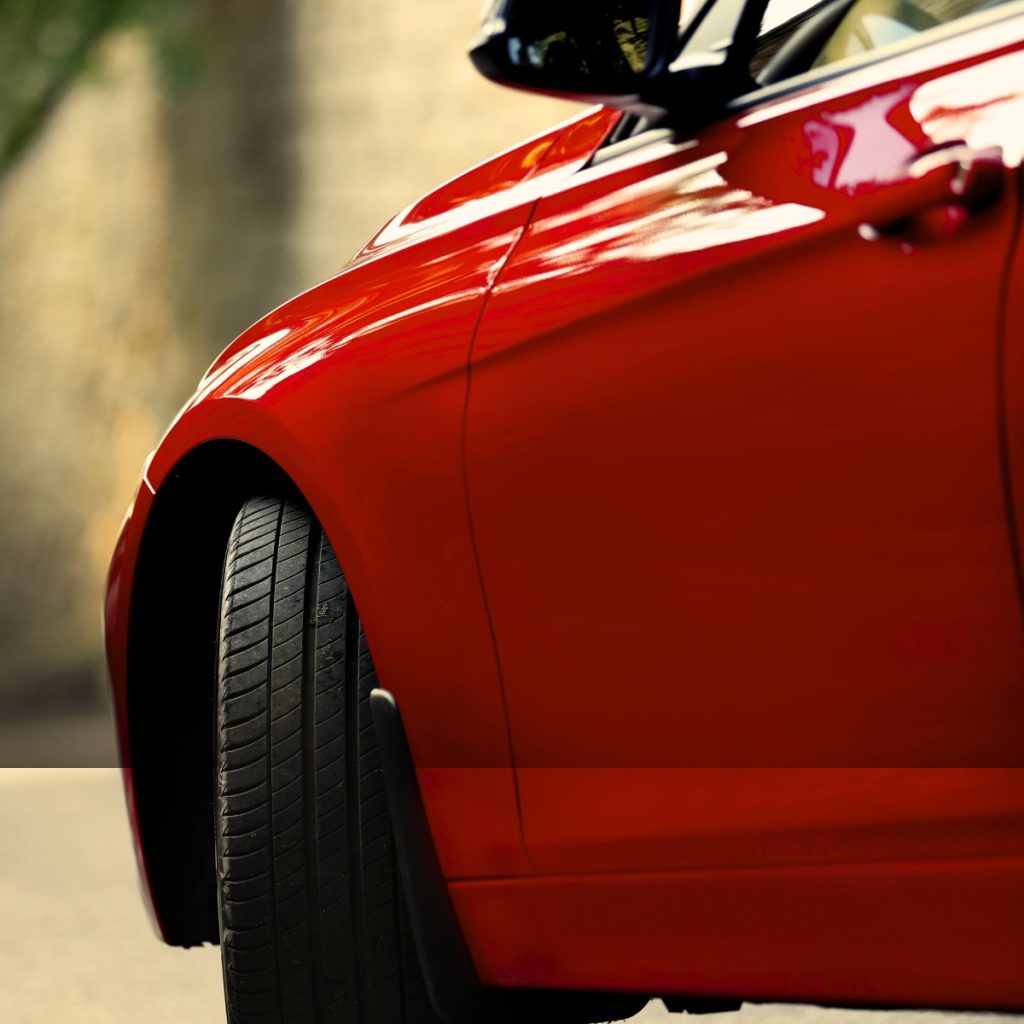
RIM coating benefits
Other than aesthetics, RIM coating provides a number of other benefits: protection against moisture, sunlight, chemicals — which would otherwise degrade the materials — and abrasions associated with daily use.
Generally, a two-component polyurethane (PU) is used for RIM coating, with color being added as desired. This material has a unique, often unnoticed feature in that it is “self-healing.” This means that should the surface be scratched, the material can repair itself, provided that the underlying thermoplastic is not also harmed. When the scratch occurs, the damage causes a release of micro-capsules which, on exposure to the contained catalyst, react and polymerize to reseal the gap. The reaction, while not instant, restores the surface to its original unblemished state.
As automotive technology advances, more and more sensors in exterior parts are being incorporated to help drivers remain alert to their surroundings, and RIM coating becomes more important. Self-driving cars, for example, rely heavily on multiple sensor types — radio-based (radar), vision-based (cameras), and light- & laser-based (LiDAR), among others — to construct a picture of the environment and react accordingly. To remain effective, these sensors need protection against a multitude of external factors, everything from pebbles in the road to unpredictable ricocheting hail, and RIM coating is an excellent choice for doing so.
This combination of aesthetic and protective benefits has shown RIM coating to be an effective, versatile solution for the automotive market, and despite its modest beginnings, one which companies continually undertake research in to find chemistries with a higher performance to gain a competitive edge.
Cannon RIM coating solutions
Over the past 15 years, Cannon has closely followed the evolution of the RIM coating process and its associated chemical systems. Whether transparent or infused with color, our range of RIM coating equipment offers clients unparalleled solutions for processing reactive polymers with the versatility necessary to adapt to the ever-changing and highly competitive automotive market. The standard combination of equipment involves a A-Compact HT dosing unit, LN 5/3 mixing head, and, if color is involved, a ChromaFeed system. Like all of Cannon products, each is customized to match the client’s exact needs and chosen process.
The Cannon A-Compact HT, designed to process resins requiring high temperatures (60-100°C), is particularly suited for RIM coating and HP-RTM applications as well as manufacturing products made of polyurethane elastomers and epoxy resins at high pressures. It processes chemicals with extreme precision and is equipped with a high-efficiency degassing system that includes a vacuum pump.
Revealed in 2024, our newly-improved LN /3 series of mixing heads are the result of their vast experience in designing and manufacturing equipment for specific applications and processes along with feedback and contributions from industry stakeholders: customers, raw material suppliers, mold-makers and injection molding machinery manufacturers, to address their needs. The mixing head now features a smaller, more compact design — ideal when combining polyurethane RIM with thermoplastic injection molding. It is quicker to affix to the mold and mixing pressure is adjustable without removing the head from the mold. A rational hose distribution ensures operators can easily access the injectors for a quick, effective and unobstructed color change.
The ChromaFeed CCS HT color dosing system allows for precise color injection directly into the mixing head, even at high temperatures, guaranteeing a smooth, uniform, and aesthetically colored part. Before blending, the polyol remains a neutral color inside the foaming tank.
The design and performance of Cannon equipment meet the specific needs of industry players and are adaptable to any injection molding machine on the market.