Authors: Andrea Bartolini (Cannon USA), Giorgio Molteni (Cannon Italy)
Polyurethane dosing equipment manufacturers face more and more stringent requirements in the contemporary marketplace, due to the fast progress on the chemistry side and increasingly sophisticated requisites by manufacturers and their suppliers. High flexibility in industrial production is pushing the technology of mixing and dosing towards levels of technical excellence never reached before.
The purpose of this paper is to share with the industrial technical community the latest achievements in high-pressure polyurethane mixing from the Cannon Group’s point of view. From automotive applications, where flexible foams require mixes composed of multiple streams, the building and furniture industries, to growing segments such as elastomers for shoe soles applications, the well-established FPL mixhead series is still widely used, with the possibility to have the third color stream along with polyol and isocyanate in the mix. We will proceed presenting the maturation of the Quick Color Change (QCC) technology, combined to the legacy of the L-shaped mixheads. A brand new range of groundbreaking heads has been refined, defining new opportunities for the quick change of a third component, color or any other additive, directly in the mixing head and recycling through a dedicated nozzle. With the 2QCC variation, today it is easy to foresee the quick change of a third and a fourth component, without wasting a single shot for flushing the mixing chamber. Different sizes and models are now readily available for QCC and 2QCC blocks, including 8, 10 and 12 mm mixheads. With the FP2L mixheads we can offer another fascinating alternative to the use of multiple colors with complex but effective mixheads provided with 2 different mixing chambers where up to 4 different streams can get together (polyol, iso and 2 colors possibly). Moreover, the development of a 4QCC quick change of up to 4 different colors/additives is underway for such mixheads. Finally, we are going to present the multi-awarded AX’s most impressive features, making this mixhead the most versatile invention in the market for TIER1s flexible foam fabrication. Today this mixhead is capable of dispensing up to 7 different components, according to a free selection of 1 axial and 6 radial streams, characterized by low weight and a compact design, modular injection and variable adjustment of total output. A multi-position stroke adjuster helps to achieve a more consistent laminar flow, while the self-cleaning piston is now able to open in less than 0.4 seconds for an overall cycle time shorter than a second.
The Cannon group has since established many years of international multi-disciplinary activities for the development of state-of-the-art mixing technologies to be able to look at the future of polyurethane processing with absolute confidence, contributing to driving innovation and offering solid solutions for the most complex goals. What is disclosed in this document is the result of years of intense R&D and laboratory activities.
INTRODUCTION
The mixing head is the most critical part of any polyurethane metering machine, the most expensive and delicate. Manufacturers are forced to refine every single process detail, focusing on mixing more than anything else, in order to achieve the desired final part’s quality. Nowadays a huge variety of processing applications require the availability of a large family of mixing heads. The mixhead ranges from applications concerning micro shots, with flow rates in the order of a few grams per second or even fractions of a gram per second to more than 10,000 g/s, in low or high-pressure, from the traditional 2-stream systems to the extremely challenging 6 to 7-stream foam. The requirements to satisfy include high-production rate, faster and faster polyurethane formulations, high repeatability, excellent temperature and nearly perfect output control.
A very important aspect driving the development of the specific technologies illustrated in this document is the growing demand for simpler, high-efficiency plants with minimum manual operation, nonetheless offering high flexibility. Nowadays, it is imperative to be able to guarantee the opportunity to manufacture several different parts within the same production line, whether it is a racetrack (or carousel), a turning table or any other high-output machinery integrated with the traditional metering units. The increasing demand for flexibility in the number and diversity of streams, including colors, for polyurethane processing applications has brought the development of a new generation of reliable multi-component mixing heads capable of performing sequences of shots with different colors. A wide range of sophistication allows the possibility to comply with a variety of technical requests including the convenience of introducing colors on/off, quick switch up to 4 different colors and the opportunity to recirculate the pigment, if not used.
As a brief introduction on the main technologies associated to different ways of applying colors into the polyurethane mix, we can distinguish different techniques:
- Traditional FPL L-shaped mixheads: provided with a single color port, it is possible to use up to 4 different colors using a ‘quad block’ connected to the mixhead. This module can be connected to up to 4 independent color units for dispensing each pigment separately. Switching from a color to another usually requires a flushing shot to clean the mixhead from the previous formulation. This is necessary because there is a single pouring channel connected to all four color ports.
- FPL QCC technology: very quick change of formulation from color on to color off (and vice versa) using a dedicated color injector. Flushing is not necessary because the module is connected directly to the mixhead’s mixing chamber and there are no areas where residuals from the previous shot can affect the next one. However, to apply more than one color, it is required to manually (or automatically) replace the color injectors.
- FPL 2QCC: mixing head provided with one mixing chamber integrated with 2 color injectors. No flushing is required in this case as well. There are no operational differences between QCC and 2QCC. They use different types of injectors, for reasons related to the space available.
- FP2L 2QCC: the technical concept is the same as the QCC above. The difference is in the fact that the FP2L mixheads are provided with 2 mixing chambers and a common pouring area. Each mixing chamber can be connected with a QCC block. No manual intervention is required. It is possible to move from a formulation to the other, each of them with a color on or off automatically.
- FP2L 4QCC: still in early design, 2 mixing chambers with a double QCC block provided with 2 color injectors each. Like every QCC implementation, no flushing is necessary and no waste of material is needed in between formulations.
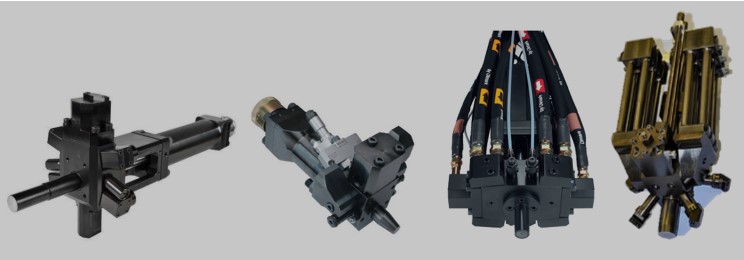
The new FPL SR series has the ability to introduce a third stream axially, a quite interesting addition for both flexible and rigid foam production. This new generation of FPLs has further improved the characteristics of laminarity, operational longevity, seals’ durability with larger features and a special hammer-shaped rod.
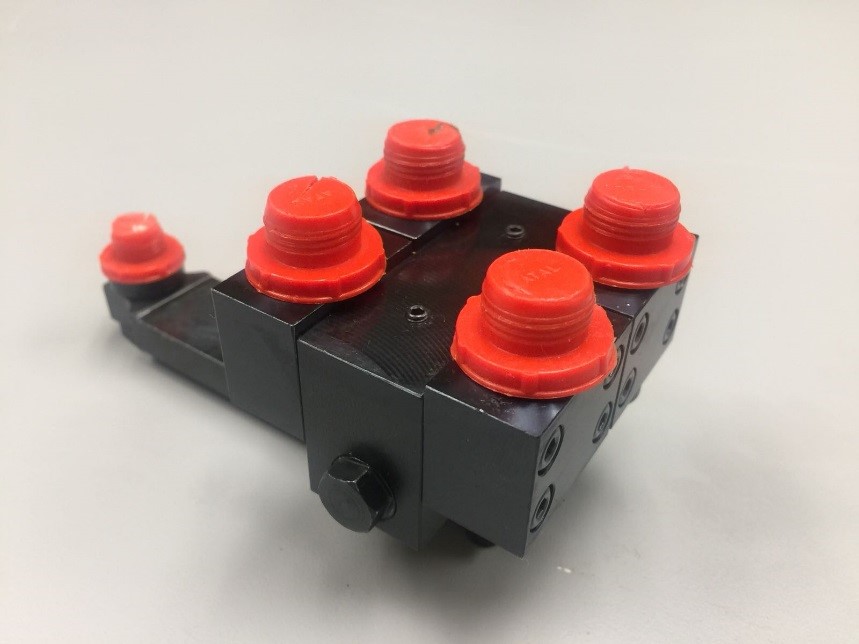
The QCC (Quick Color Change) family was born from the need to dispense color directly into the mixing head along with the other main components. The change of color takes place when a color injector is replaced by another connected to a different color unit, a dedicated standalone dosing group for every pigment involved in production. The core products developed around this concept have been:
– FPL 10 QCC (10 mm cleanout piston diameter, 1 polyol, 1 isocyanate and 1 color available)
– FP2L 10 2QCC (10 mm cleanout piston diameter, 2 polyols, 2 isocyanates and 2 colors available)
The color can be injected directly in the mixing chamber and recirculates through a dedicated hydraulic injector that can be changed without flushing.

Another mixhead with a double mixing chamber (FP2L) for color application is almost ready to be placed in the market. This new mixhead will be capable of quickly switching among 4 colors. Manufacturing processes involving steering wheels, flexible automotive components and elastomer are expected to particularly benefit from this new quadruple color head.
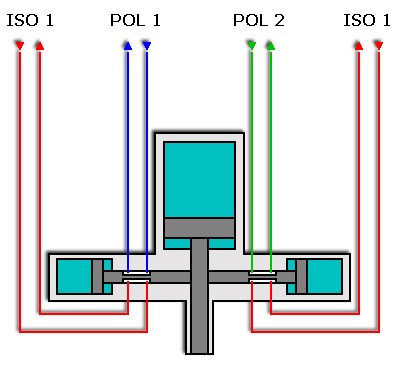
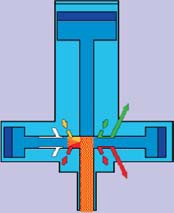
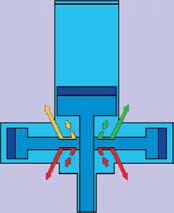
Figure 4: FP2L streams, recycling and pouring phases.
The need to limit costs lead to the greater use of automation, in order to reduce the use of manual labor and operate frequent and efficient changes of formulations, minimizing down time by eliminating the waste of costly raw materials as much as possible. This premise brings us to the design of the AX generation of mixheads.
Each circuit is totally independent and the mixhead can keep the components separated until they reach the mixing chamber altogether. In this way, cross-contamination is impossible. Moreover, each component can be provided with individual high-pressure recirculation control and can be operated only when required. Low-output components like colors are typically fed axially and recirculate as well. The time separating two consecutive shots can be as short as half a second. Pour pressure control can be effectively managed with different setups including closed-loop control of the injection pressure via hydraulic servo valves and feedback control.
Color can be introduced in the polyurethane mix in different ways, each representing a different level of sophistication and investment. The specific mixhead and its configuration is regularly selected after identifying the proper region from the chart below, which distinguishes the following cases:
- Axial injection without recycling
- Axial injection with recycling
- Direct injection in mixing chamber (with QCC technology)
- Direct injection as an independent stream (AX mixing heads)
INJECTION | MIXING HEAD | COLOR SYSTEM | RECYCLE |
AXIAL | FPL Color Injection | Piston Pump | No Yes |
DIRECT | FPL QCC | Pump | Yes |
DIRECT | FPL 2QCC | Pump | Yes (automatic or with switch) |
DIRECT | FPL AX | Pump | Yes |
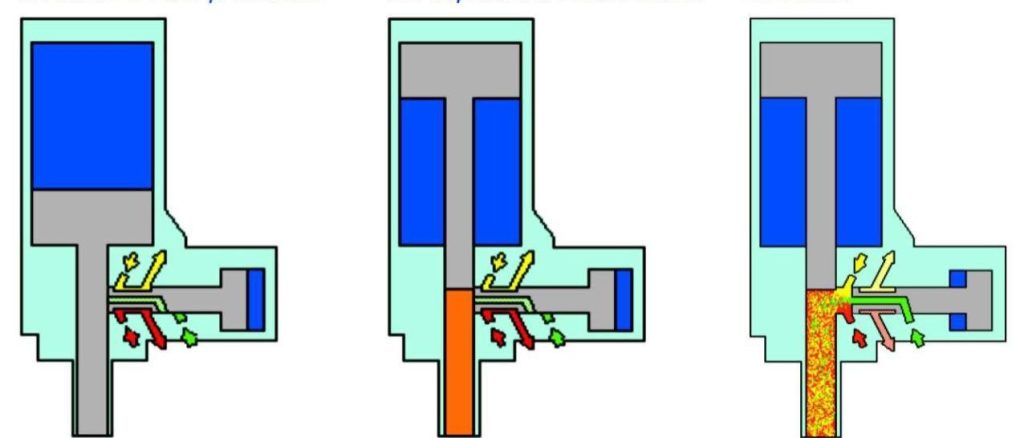
‘L-SHAPED’ HEADS
The newest and patented SR design represents a clear intention to further increase the lifespan of the new generation of mixheads, up to 3 times. This is why the mixing chamber is made by a single piece with no joints between parts, in order to avoid any issue involving misalignment and accumulation of structural loads in proximity of connections between components. A much longer nose and larger mixing chamber offer better laminarity performance. Moreover, the self-cleaning rod presents a ‘hammer’ shape in order to reduce the sliding surface between the piston and its housing to reduce heat-related friction and, therefore, improve the operative life of the head. The SR family can be used successfully from low-density rigid foams to flexible polyurethane foams.
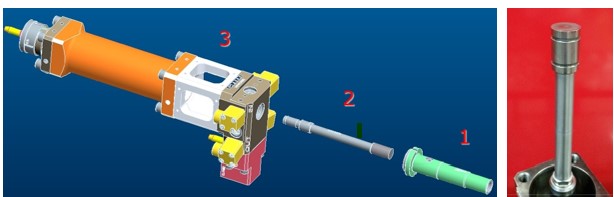
By means of a narrow duct grooved axially through the mixhead’s cleanout piston, the color can be conveniently introduced in the highly turbulent mix directly in the mixing chamber, with the complete blending of pigments that often are characterized by high viscosity. Colors can be interchangeable with a flushing shot between different batches of production, to remove any previous color residual.
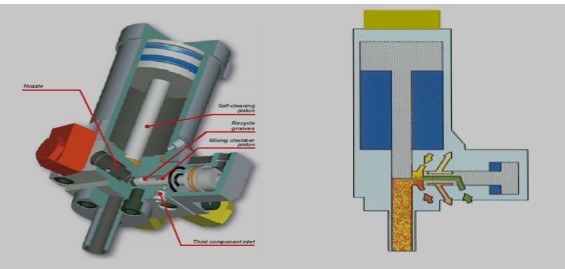
FPL mixheads are also available in the AN (axial needle) version. These special mixheads are provided with a needle to control the flow through the axial duct.
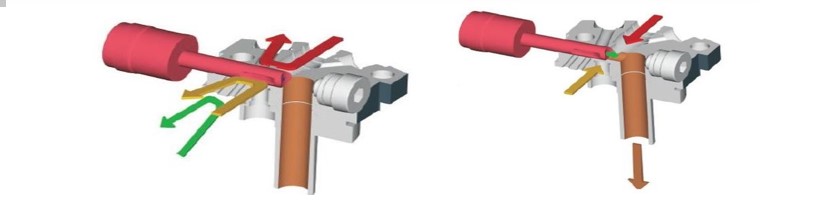
Dispensing color through the axial needle allows a more limited investment, while it is possible to use up to 4 different colors or more, if required. The polyol does not need to be pre-mixed. A cleaning shot is necessary because the axial channel is common for all the color injectors installed.
THE FPL QCC
The QCC option for the FPL mixheads was introduced to satisfy highly demanding requirements for applications like automotive steering wheels production. The system was born to be able to meter one color directly into the pouring chamber. Without modifying the mixhead, it is possible to have shots with or without color. To be able to run alternate campaigns of different colors, a 2QCC block can be used instead. Both assemblies can install color injectors connected to independent color units; most applications do not require anything more complex than the possibility to manually switch from a color injector to another. However, today it is also possible to implement an automatic switching system that operates in relation to the different recipes, shot after shot.
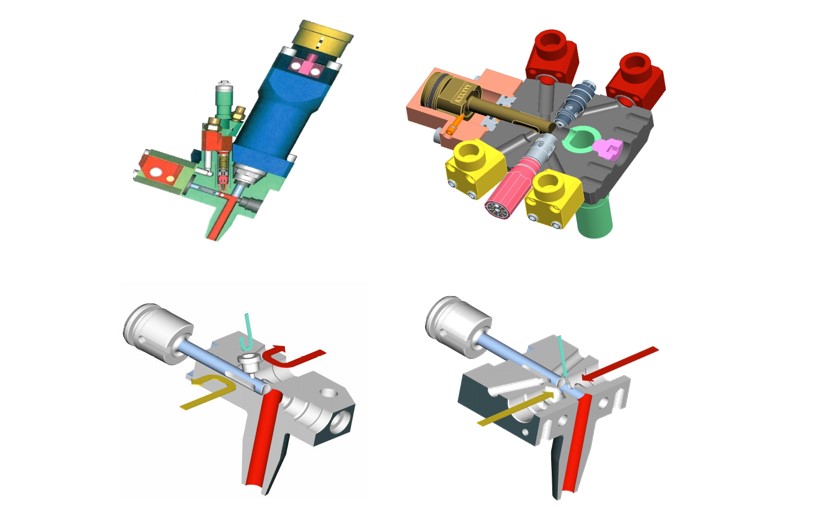
A test performed on an FPL10 QCC took place to verify the quality of alternate consecutive shots with and without color. While the main components, polyol and isocyanate, were dispensed at 145 g/s (respectively 185 and 175 bar), the color was introduced in the mix at barely 3 g/s (22 bar).
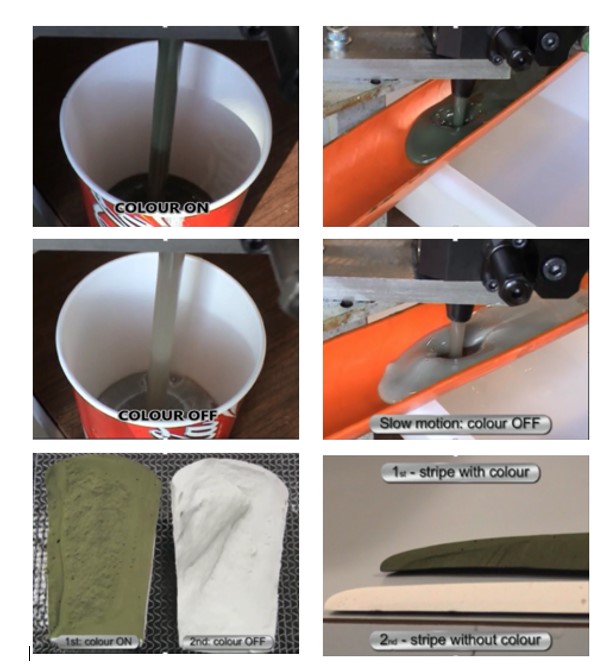
An interesting implementation of direct color injection can be achieved with the new FPL12 2 QCC, a 2-stream mixhead created for the quick switch of a third and a fourth component (mainly colors but other additives can be used successfully as well). The two colors are injected through opposite injectors that can be changed without the need of flushing shots.
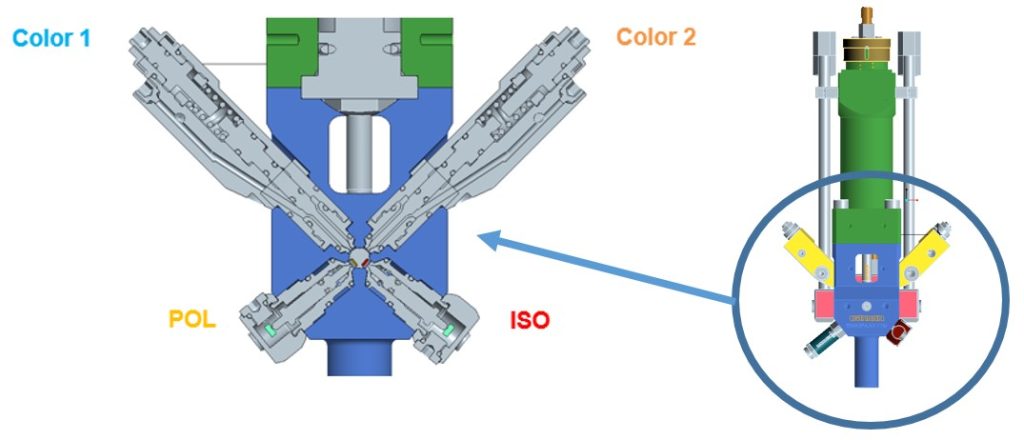
The color injectors, being independent and hydraulically operated, allow the possibility to precisely control the opening and closing, in order to correctly synchronize the mix for final part’s quality.
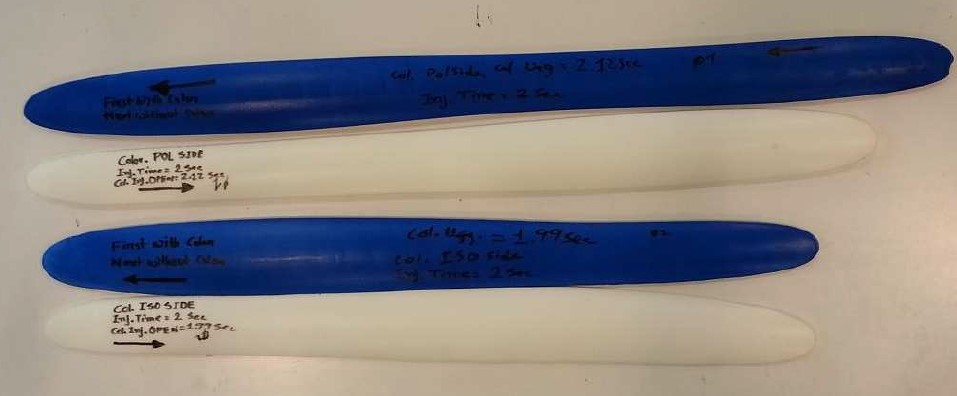
AX MIXHEAD
Within the AX family, the AX 14/4 mixhead is the smallest developed. Like its designation suggests, four different streams can be introduced into the mixing chamber, while two injectors can be dedicated exclusively to colors and the other two to polyol and isocyanate. This head can be hardened for the utilization of abrasive materials.
The six component AX can meter different combinations of streams and with full high-pressure recirculation of each of them. Four components can be injected radially and recirculated at high-pressure, while two low-output and low-viscosity streams can be introduced axially; axial components recirculate directly in the head as well, as the figures below demonstrate.
At the same time, the AX 22 was developed as the only mixhead capable of dispensing at the same time up to 7 streams, 6 radially and 1 axially. The seventh component can be metered on/off when desired. The position of the cleanout piston is regulated by means of a proportional valve that determines the exact location of the piston during both the opening and closing phases, to optimize the mix. The new generation of AX heads features the switching valves installed directly on the mixhead’s blocks. The development of the head was completed in 2014 and at the end of the same year the AX 22 6+1 components became operative offering noteworthy mixing performance, short cycle times and high shot frequency, easy installation and maintenance. Nowadays, the AX mixheads are widely used for automotive flexible foam applications to realize multi-hardness, multi-density seating products and was awarded in 2017 the “Technology and Development Award” by Toyota Boshoku.
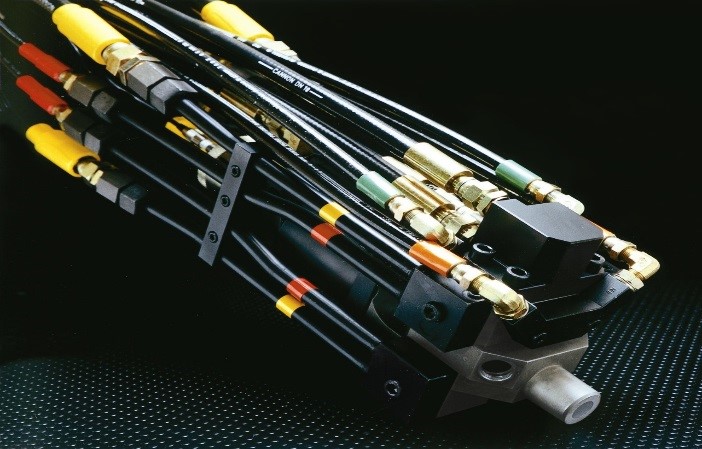
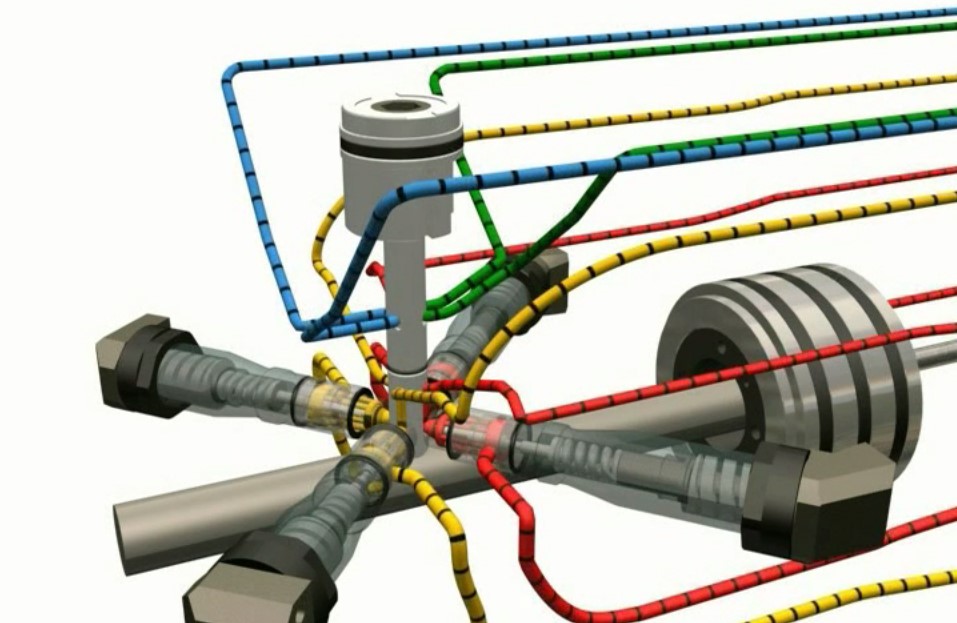
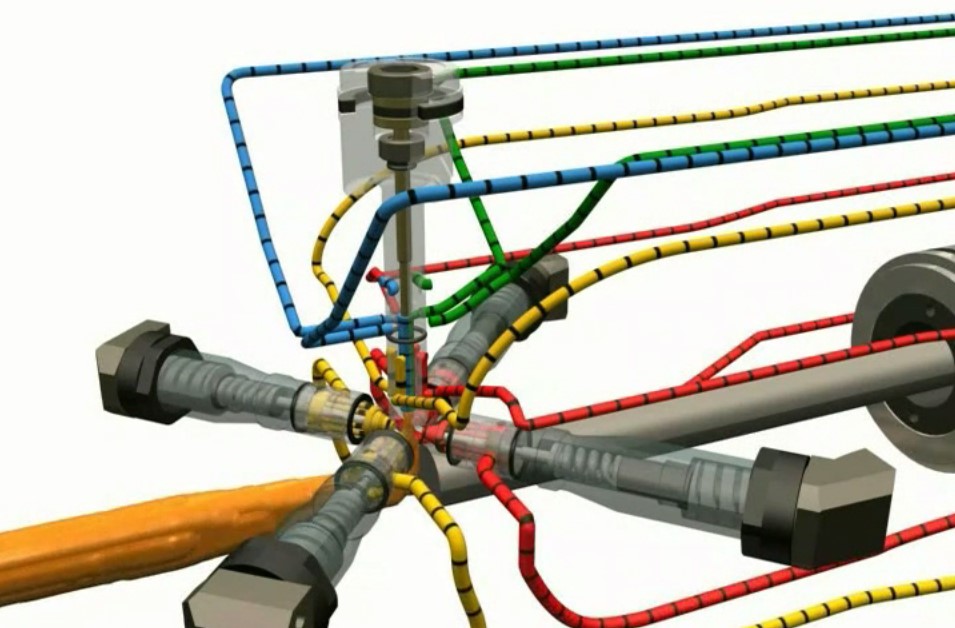
In a recent experiment, three different colors of integral skin polyurethane foam were obtained using only four components, dispensed in different combinations and proportions: isocyanate, blue polyol, black color and flame retardant. Spring loaded injectors without remote control, therefore, requiring the pressure to be set manually, were used while the final parts required a range of flow rates from 160 to 200 g/s. Polyol and iso’s metering parameters were kept constant for all the three cup shots, while varying the percentage of black color. It was possible to obtain black parts (12% of black color in the mix) and grey ones (3%). Tests like these prove the versatility of such mixheads. Interestingly, the sequence of shots, from the blue to the grey with the black in between, was preprogrammed in the control panel with the goal of having the mixhead automatically dispensing different recipes. It is possible to notice from the picture below how just a few seconds were separating one shot from the other just by looking at the curing progress. The ratio between iso and polyol was 0.45 in favor of the iso; both main streams were poured at 190 bar, the flame retardant at 70 bar.
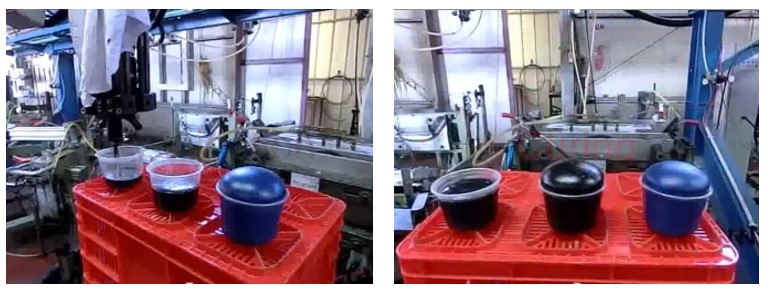
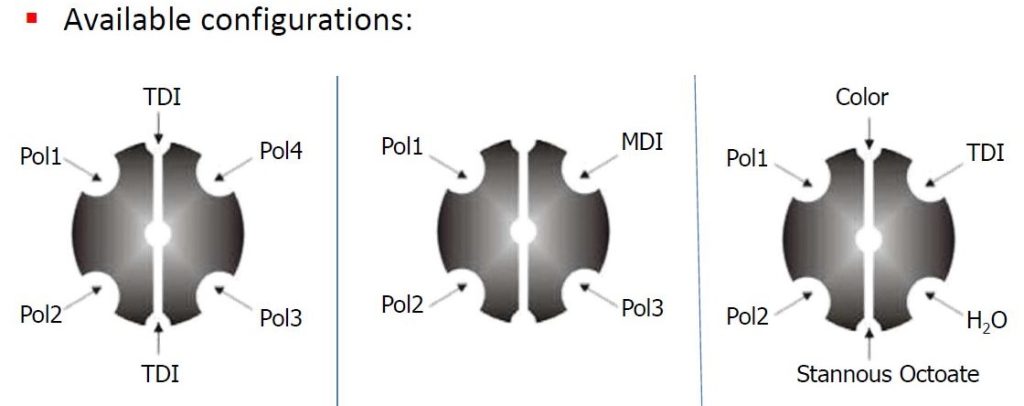
The AX multi-component head was invented to cover mainly seating applications with requirements demanding the possibility to mix TDI isocyanate and up to 3 polyols as well as the possibility to pour MDI and TDI at the same time. These heads offer the opportunity to complete a whole pouring cycle in less than 1 second at a typical laminar flow rate range from 90 to 800 g/s. Some features that characterize the success of the AX series are similar to the ones featured by the SR heads: hammer-shaped cleaning rod, longer stroke and improved materials.
The AX family is well represented in particular by the AX 14/4, AX 18/4 and AX 22/6 models. The 14/4 was designed for the use of four radial streams, relatively small outputs with an ideal laminar flow of 350 cc/s and readily available, even with hardened materials for heavy duty chemistry.
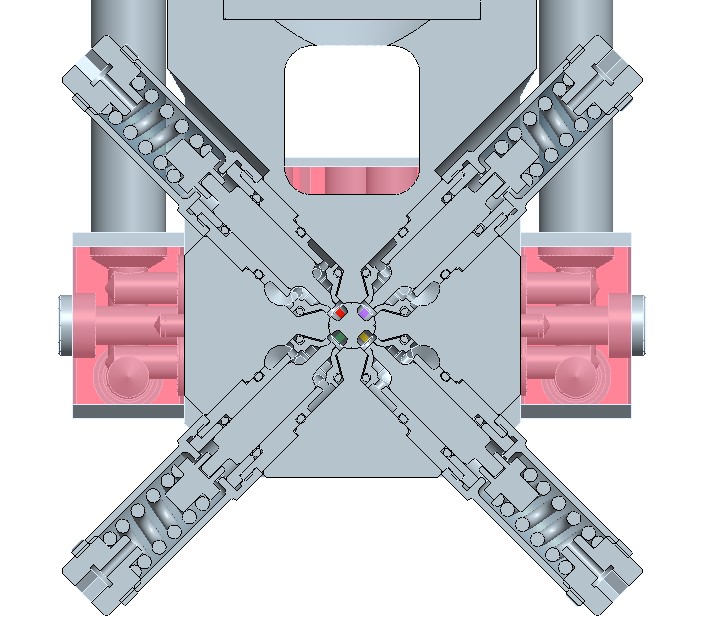
The 18 mm AX18/4 is a similar larger version, still capable of dispensing four radial streams, one axial, for a total of five components and up to 650 cc/s of laminar flow rate.
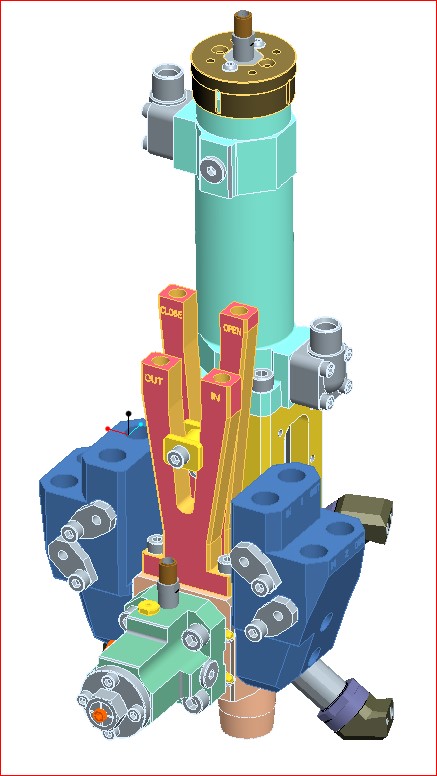
The AX 22 is the ideal mixhead for flexible foam applications; more specifically, it was created to face the challenging requirements coming from the automotive seating industry. With six radial and one axial component, nothing can offer higher flexibility in the market today and a wider choice of stream combinations. Almost all the AX22 mixheads produced are operating with automotive flexible systems, which require the possibility of dispensing the more conventional 2-stream mixes as well as complex and heterogeneous formulations made by up to seven components. All this while guaranteeing outstanding mix quality and high frequency of shots for fast operation with cycle times shorter than 1 second. Laminar flow rates with this head can reach 700 – 800 cc/sec.
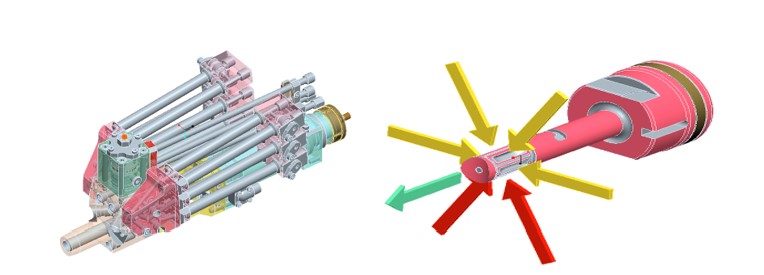
Remarkably, as well as the AX 18/4, this mixhead features high-performance stream distributors integrated into the components blocks. Originally the distributors were installed before the mixing head, on the robot. In this way it is possible to save up to 15 kg in weight, allowing a much easier setup and operation.
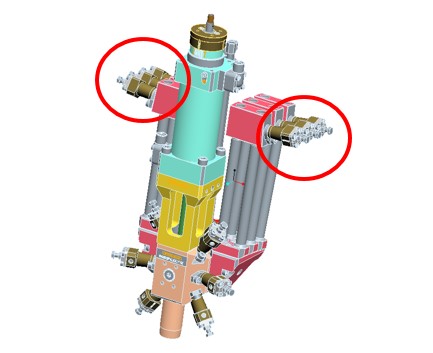
Another useful feature is the multi-position hydraulic stroke adjuster. An LVDT sensor measures the opening position of the cleanout piston, which can be regulated shot after shot to change the mixing dynamics and find an optimum mix for every chemical system and production process.
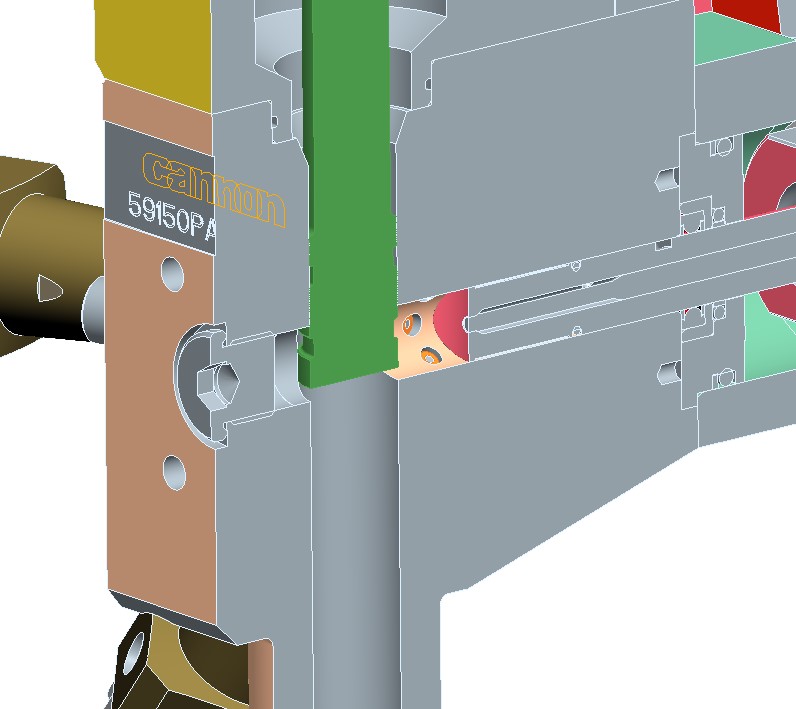
For those applications where a frequency of shots in rapid sequence is required, especially with different outputs and ratios, the mixing pressure becomes a critical factor to control. Different control designs came to light in regards:
- Re.Co. (Remote Control) Injectors: today two versions of Re.Co. are available:
- “Re.Co. on/off”: the injector can be totally closed or totally open according to the position needed, to select and deselect the chemical needed for each shot. Special spring-loaded nozzles can be used to keep the pressure constant even in situations where the output varies between 10 and 15%.
- “Re.Co loop”: remote pressure control based on a closed loop system capable of controlling the injection pressure through proportional hydraulic valves. Pressure transducers maintain constant pressure even during flow rate variations.
- Special spring-loaded nozzles can be used to keep the pressure constant even in situations where the output varies between 10 and 15%. The fixed position of the injectors can be achieved by means of hydraulic valves pre-established positions.
Not only is the Re.Co. setup capable of keeping the injection pressure stable, but the multi-components mixing systems like the AXs, it can select on/off the components to be injected in the mixing chamber, partially opening or completely closing each specific injector. When the nozzle is closed, the component is recycled through high-performance stream distributors, hydraulically driven and provided with a pressure regulator valve. With the latter solution, it is possible to change formulation in 0.7 seconds. The use of hydraulic valves allows a faster switch among different formulations, with the hydraulically operated orifices adjusting automatically to the pressure input. The Re.Co. along with a state-of-the-art closed loop feedback control system allows a variance of ratio and shot weight no larger than +/- 1%. The Re.Co. can only be installed in the radial components of the AX. The Re.Co system can be used to pour color in specific cases.
On the other hand, the spring nozzle systems consists of providing fixed pressure control using hydraulically driven nozzles. Similarly to the Re.Co. case, each nozzle selects the component on/off and controls the injection pressure during pouring.
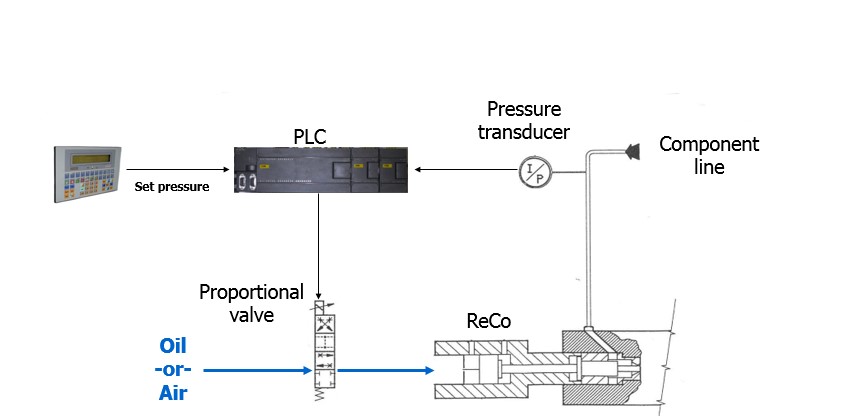
In case high-viscosity and/or abrasive streams are used (color often contains an abrasive filler commonly known as ‘carbon black’) the mixhead is subjected to hard metal sintering and hardened parts (injectors, spools and bushings) are installed.
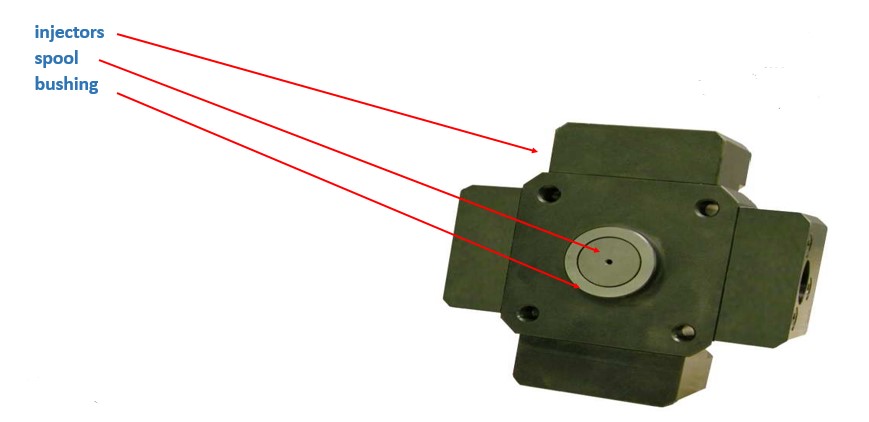
COLOR DOSING UNITS
With the goal of being able to offer a complete technology package and to effectively control the use of pigments for several types of situations, the manufacturer is capable of offering not only mixing capabilities but also specific dosing units designed and produced exclusively for colors. Dedicated metering units were developed to be connected to the vast range of multi-stream mixheads discussed so far. These machines are provided with their own tanks, pumps (or plungers for heavy-duty materials) and controls. There are color systems of different sizes available, some of them offering the possibility to recirculate the color back to the tank.
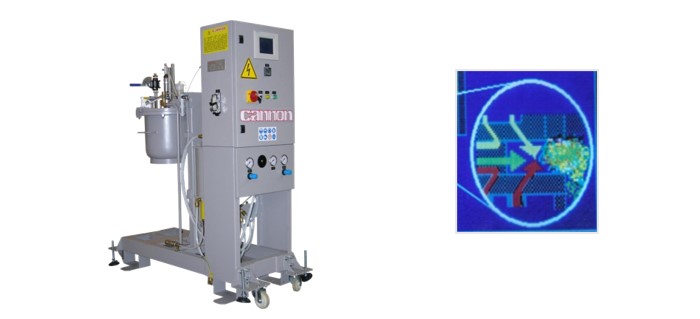
The unit doses the colored paste (to be diluted with polyol for a certain viscosity reduction) so that the color is directly mixed to the two basic components at the mixing head. While the CCS is a unit suitable for dosing color directly in the mixing head, but without the possibility to recycle the material, the Color Unit (CCU) is featured with the recycling capability.
CCS 100 | CCS 300 | ||||
Metering Cylinder Volume | 100 cm3 | 300 cm3 | |||
Output (Air Pressure 2 bar) | 14 cm3/s | 14 cm3/s | |||
Output (Air Pressure 4 bar) | 20 cm3/s | 20 cm3/s | |||
Output (Air Pressure 6 bar) | 25 cm3/s | 25 cm3/s | |||
Re-filling Time | 3 s | 5 s | |||
Power | 0.3 kW | 0.3 kW | |||
CCU 1 | CCU 3 | CCU 12 | |||
Pump capacity | 1 cm3/rev | 3 cm3/rev | 12 cm3/rev | ||
Output range (*) | 0.45 – 2.7 g/s | 1.35 – 8.1 g/s | 5.4 – 32.4 g/s | ||
Power | 1.5 kW | 1,5 kW | 2 kW |
CONCLUSION AND FUTURE DEVELOPMENTS
This work represents a collection of insights about the functioning of the different generations of mixing heads dedicated to the utilization of colors, part of multi-stream mixes. Future accomplishments will likely be centered on the development of mixing heads provided with a double mixing chamber (FP2L style) with a 2QCC implementation per side.
Color technology has proven to be successful worldwide when implemented, from automotive seating and steering wheel production to refrigeration and countless varied applications. Multi-component mixing heads and all the equipment necessary to correctly perform not only the mixing and pouring phase, but also the storing and metering of the color streams have immediately gained great success in the industrial community with several projects completed and many more in the process of being defined and implemented. The range of technology available today is wide enough to be able to satisfy many requirements, characterized by different budgets available, production output, parts complexity and process sophistication.
It is always convenient to plan some laboratory activity before completely defining any equipment final configuration and components selection. The polyurethane community can definitely benefit from a complete and convenient investigation of all the nuisances that can distinguish success from failure. Our industry demands more and more the full collaboration and availability of the equipment manufacturer, who needs to understand and immediately comply with the evolution of production dynamics and the newest chemical systems created by the raw material suppliers.
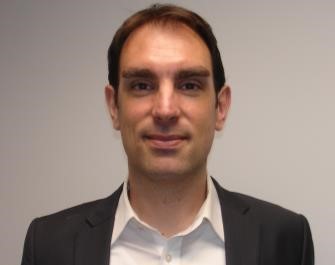
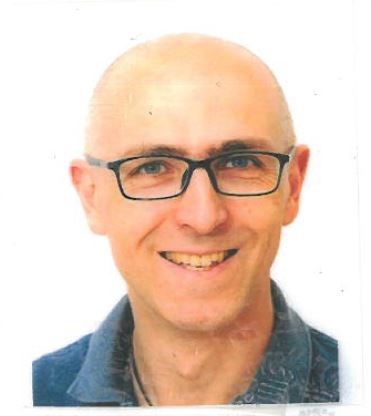