Die in-situ Polyurethan Beschichtung ermöglicht eine prozessintegrierte Oberflächenveredelung von spritzgegossenen Bauteilen. Gemeinsam mit dem PCCL arbeitete NMB daran, die Qualitätssicherung dieser Technologie zu ermöglichen, indem Fehlerquellen identifiziert und die Fehler selbst mittels künstlicher Intelligenz erkannt werden.
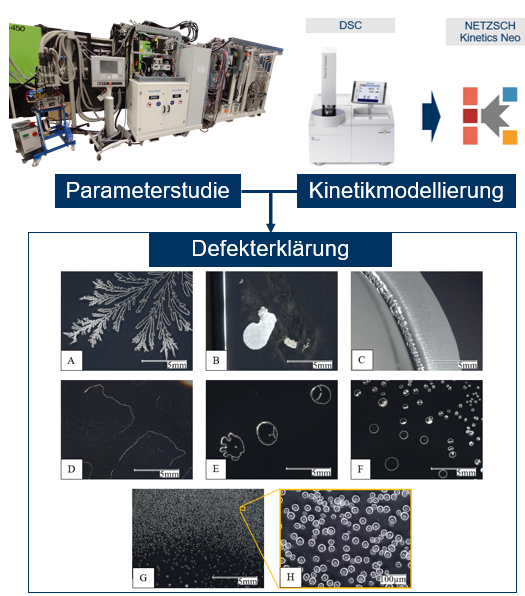
Ziel eines erfolgreich abgeschlossenen öffentlich geförderten Forschungsprojekts der Neue Materialien Bayreuth GmbH (NMB) in enger Zusammenarbeit mit der Polymer Competence Center Leoben GmbH (PCCL) war es, Fehler auf polyurethanbeschichteten Oberflächen erkennen und erklären zu können.
Hierzu wurde der In-Mold-Coating (IMC)-Prozess in der NMB-Pilotanlage implementiert, wobei ein Wendeplattenwerkzeug in Kombination mit einer Spritzgießmaschine mit 450 t Schließkraft und einer mobilen Hochdruck-Dosier-Anlage für Polyurethan (PUR) zum Einsatz kam. Hierbei wird im ersten Schuss der frei geformte 3D-Träger im Spritzgussverfahren hergestellt. Anschließend wird die mittlere Formplatte um 180° gedreht und die Sichtseite in einem zweiten Schuss mit PUR überflutet.
Das Projekts ermöglichte folgende zentrale Ergebnisse:
- Aufdeckung prozessbedingter Fehlerquellen
Durch eine umfassende Parameterstudie des PUR-Beschichtungsschritts konnten zentrale prozessbedingte Faktoren identifiziert werden, die zu Fehlern führen. Deren Auftreten in bestimmten Bereichen wurde klassifiziert.
2. Erstellung eines Aushärtungsmodells
Ein zuverlässiges Aushärtungsmodell für hochreaktive PUR-Beschichtungssysteme wurde auf Basis der Differential Scanning Calorimetry (DSC) zur Datengenerierung entwickelt und durch in-situ Dielektrische Analyse (DEA) validiert. Dieses Modell ermöglicht ein besseres Verständnis des Aushärtungsprozesses und damit des Fließverhaltens im Werkzeug, was zu konsistenteren und qualitativ hochwertigeren Ergebnissen führt.
3. Verknüpfung von Fehlern mit Prozessparametern
Die Verbindung zwischen dem Aushärtungsverhalten und spezifischen Prozessparametern konnte das Auftreten bestimmter Fehler erklären. Dieses Wissen versetzt Hersteller in die Lage, gezielte Anpassungen vorzunehmen und die Fehlerwahrscheinlichkeit zu reduzieren.
4. KI-gestützte Fehlererkennung
Durch den Einsatz künstlicher Intelligenz entwickelte das PCCL erfolgreich ein KI-basiertes System zur Fehlererkennung. Dieser innovative Ansatz ermöglicht eine Echtzeit-Qualitätskontrolle, stellt höchste Produktstandards sicher und optimiert gleichzeitig die Produktionsabläufe. Dieses Vorgehen ist in der folgenden Abbildung zu sehen.
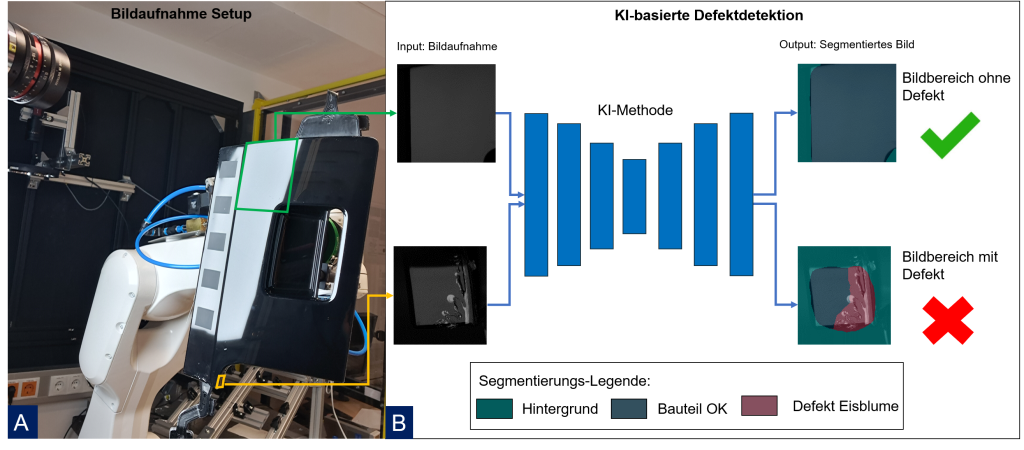
B) Die aufgenommenen Bilder werden mit einer vom PCCL entwickelten Software verarbeitet. Die KI-basierte Defekterkennungs-Methode erhält die Bilder als Input. Der Output dieser Fallstudie sind segmentierte Bilder, in denen durch unterschiedliche Farben die verschiedenen Klassen (OK-Bereich, Hintergrund, Defekt-Bereich) dargestellt werden.
5. Reduzierung von Ausschuss und Steigerung der Effizienz
Durch ein besseres Prozessverständnis konnte die Anzahl fehlerhafter Teile erheblich reduziert werden, was zu Kosteneinsparungen und einer geringeren Umweltbelastung führt.
Das Forschungsprojekt wurde bei der Neue Materialien Bayreuth GmbH und der Polymer Competence Center Leoben GmbH im Rahmen des Kompetenzzentren-Programms COMET des Österreichischen Bundesministeriums für Digitalisierung und Wirtschaftsstandort sowie des dortigen Bundesministeriums für Klimaschutz, Umwelt, Energie, Mobilität, Innovation und Technologie durchgeführt. Beteiligt waren die Burg Design GmbH, die AT&S AG und die Krenhof AG. Das Projekt wird durch den Bund sowie die Bundesländer Steiermark, Oberösterreich und Niederösterreich gefördert.
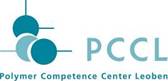
